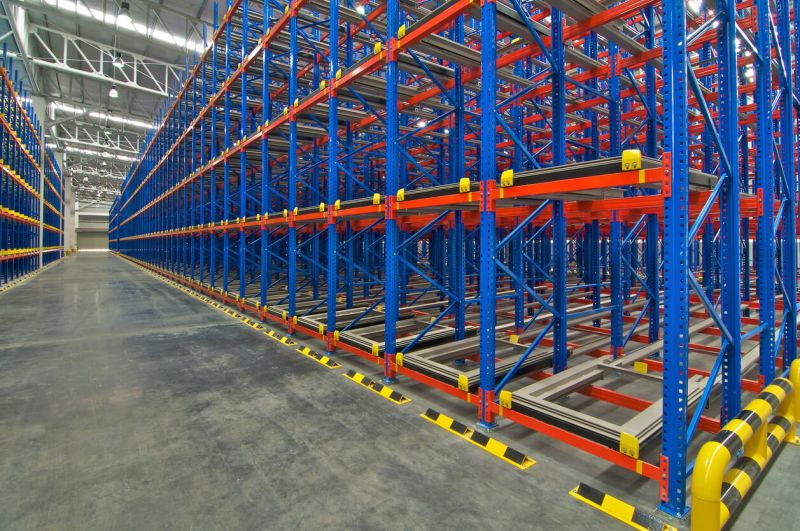
Did you know that it is mandatory to have your warehouse racking systems inspected every year?
It is crucial for any business that uses racking systems to have them inspected at least once a year, without fail, to ensure they meet Australian Standards for Steel Storage (AS4084:2012). A Risk Safety Inspection (also referred to as a Risk Safety Audit) at your warehouse or business premises ensures the protection and safety of your employees, equipment and your investment.
While having the correct protective barriers, such as post protectors, on your racking is a good preventative, damage can still occur and lead to collapse. Damage to your racking will also result in damage to your inventory, potential injury to other staff and clean-up costs. So, it is a small expense that can save you thousands in the event of an accident.
What is checked during a Risk Safety Inspection?
As part of a professional Pallet Racking Safety Inspection, Global Industrial will visit you on-site and during the inspection, we will check the following;
- Load signs
- Beams
- Base Plates
- Levelling plates
- Frames
- Splices
- Any loose, missing or dislodged racking components
- Pallets
- Any modifications that have been made.
If you have made any modifications to your racking, please let your attending advisor know so that they can check to make sure this meets the Australian Standards, as this can affect your safe working load limits.
Ensure the safety of your pallet racking systems with Global Industrial
The Australian Standard mandates inspections are carried out at least once a year, but to ensure the safety of your employees and your inventory, we recommend more regular checks. For more information on how to carry out your own regular checks between professional inspections, ask for our Printable Weekly Racking Safety Checklist.
To book your Racking Safety Inspection, contact Global Industrial on 1300 762 686, or via email at sales@globalind.com.au